| Transfer TableThe Challenge:
A car manufacturer needed to move heavy steel parts bins between parallel in and out conveyor lines in one of their parts distribution centers. The use of a ball transfer table was not proving to be an effective solution. The bins with a narrow steel frame base were difficult to control and the ball transfers failed more frequently than was acceptable. The manufacturer challenged their conveyor supplier to come up with a more effective product for transferring the par ts bins through the workstation from one line to the other. | The Rotacaster Solution:
The conveyor company used Magnus Mobility’s Max Performance Conveyor Rollers to solve this problem. Max Performance Conveyor Rollers use the Rotacaster multi-directional wheel to provide easy and controllable movement in all directions. The Max Performance Rollers were installed in an existing conveyor section, replacing 1.9” steel rollers as a retrofit. | 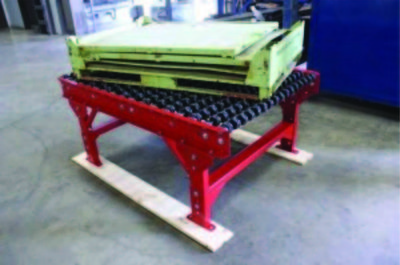 | The Results:
The parts bins are now easy to control and move, requiring less force by employees than the ball transfer table. The product selected was a 32” Max Performance Roller with the Rotacaster R2-0484-99 wheel on 2” centers. Rollers were installed on 3” centers. The solution requires no power to the Rotacasters and minimal maintenance, while delivering reliable productivity.
|
|
| | Pallet Transfer StationThe Challenge:
A South African company needed a solution for a transfer table to redirect pallets at the end of a conveyor line. They needed a robust, reliable and cost effective solution with minimal maintenance needs. | 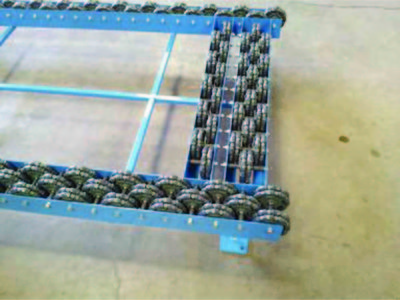 | The Rotacaster Solution:
Instead of the more traditional infrastructure and maintenance-heavy air- or ball bearing tables, the company opted for Rotacasters effectively configured around the periphery, as seen in these images. Thanks to the multi-directional capabilities of the Rotacasters the solution is simplicity itself. The complete solution requires only 64 paired R2-125mm Rotacasters and supports weights of up to 800Kg per pallet. It can be operated by a single person. The received pallet can comfortably be moved to and from the receiving table. The solution requires no power and minimal maintenance, while delivering reliable productivity.
|
|
| | Concrete Wall TransferThe Challenge:
A concrete pre-fab company in Canada needed a solution to transfer concrete walls from one assembly line to the next in their curing facility. The solution needed to be durable, cost effective and require minimal maintenance. | 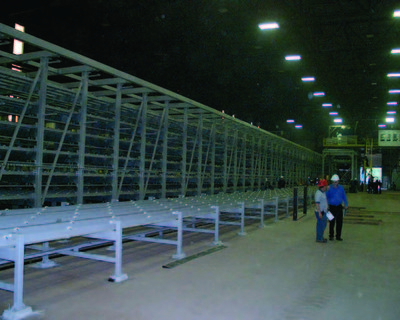
| | The Rotacaster Solution:
Instead of the more traditional infrastructure, the company opted for Rotacasters arranged along the line of- and perpendicular to the primary direction of movement. The solution required only 72 paired R2-125mm Rotacasters per transfer table. 12 tables were installed in total. Transferring the substantial wall slabs was handled by a simple chain drive requiring minimal maintenance, while delivering reliable productivity |
|
| | Steel Dollies for cargo airlineThe Challenge:
Incheon Air, a South Korean cargo airline, faced the challenge of transferring a very heavy load into the body of their Boeing 737-400 freighters. While the aircraft interior floor is equipped with ball-transfers, they are not suitable to carry the heavy point loads of the cargo. | 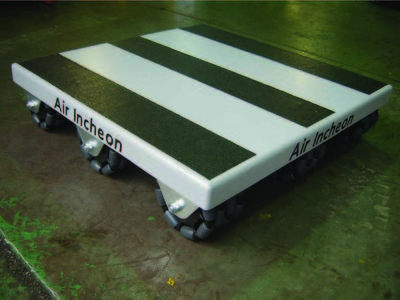 |
The Rotacaster Solution:
Air Incheon turned to Korean Rotacaster partner BNP in search for a robust multidirectional solution. In collaboration they designed and built a heavy-duty steel dolly equipped with nine Rotacaster quads. The solution enables Air Incheon to place the cargo onto four of these dollies and bring the shipment into the aircraft, negotiate a 90 degree turn and place it into the correct location to balance the load. The solution requires no power to the wheels and minimal maintenance, while delivering reliable and improved productivity. |
|
| | Manual transfer stations: Australia Post specifies Rotacaster The Problem Australia Post used ball transfer tables for manual sorting of bulky international mailbags weighing up to 35 kg. This required substantial and repetitive manual effort by operators to push, pull and rotate the bags, exposing them to potential musculoskeletal injury. | 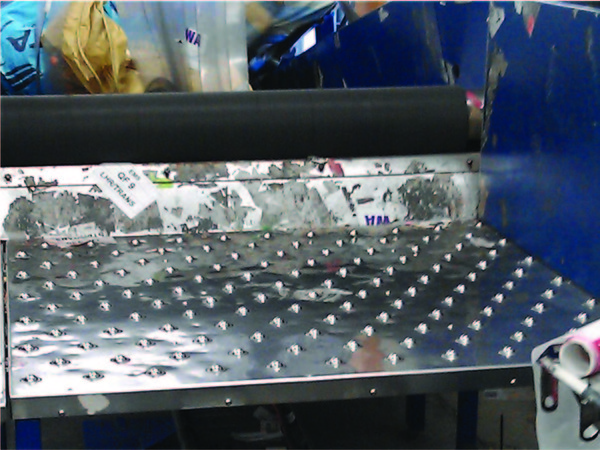
| | The Challenge: To address this issue Australia Post looked for alternative solutions that would substantially reduce operator input and exposure to risk of injury. With a targeted push/pull force of 50N (5kg) for a 35Kg bag, it was acknowledged that this target would in all likelihood require a powered solution, adding to operating and maintenance costs.The problem: Australia Post used ball transfer tables for manual sorting of bulky international mailbags weighing up to 35 kg. This required substantial and repetitive manual effort by operators to push, pull and rotate the bags, exposing them to potential musculoskeletal injury. | | Rotacaster Solution: Rotacaster proposed a manual transfer solution utilizing their 48mm Rotacasters combined with polyacetal (POM) spacer rollers. The roller’s smaller diameter was designed to provide support for the soft packaging, while minimizing friction and reducing the number of Rotacaster wheels required. Australia Post and Rotacaster collaborated on the design and construction of the transfer table. Trials were successfully undertaken at an Australia Post gateway. | | 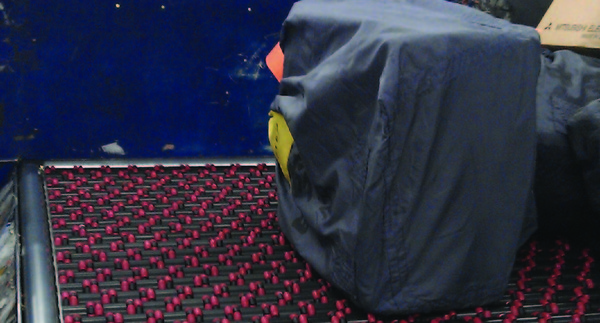
| |
Outcome: The solution resulted in a significant reduction of push/pull forces to between 40 and 70N (4-7kg) in all directions on the table. Australia Post considered this a remarkable achievement in the absence of any powered assist.
Additional Advantages: In addition to reducing the push/pull forces required, without the cost noise and maintenance associated with a powered solution, the polymer surfaces of the Rotacasters and spacer rollers have demonstrated a lower affinity to adhesion of labels and stickers from packages, further reducing down time and maintenance costs. | | Comment: Rotacaster CEO Peter McKinnon notes “Feedback from operators using the table has been exceptionally positive. And importantly, the risk of injury has been reduced. Rotacasters are proving their versatility.” Implementation: With this extremely successful trial result, the remaining transfer tables at this Gateway facility will be replaced with the Rotacaster solution, with further upgrades to follow in Sydney, Brisbane and elsewhere. | |
Type: Transfer Table, air mail Load: 35Kg (77lbs) User: Australia Post Country: Australia
|
|
View Page < Previous | 1234 | Next > |